MIG Welders
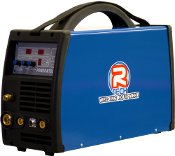 |
MIG TIG ARC Welder -Multi-Process Machine
The MTS210 Digital MIG, DC TIG and MMA welder features a high 35% duty cycle, digital
control panel for easy adjustments, memory store facility, MIG wave adjustment for fine control of
welding arc, 5KG reel capacity with 2 year warranty
- 200 Amp MIG Welder
- 200 AMP DC TIG Welder
- 175 Amp Arc/MMA Welder
- Digital Control Panel
- Takes 0.6, 0.8, and 1.0mm wire

|
 |
MIG I-MIG200
The I-MIG200 MIG welder
is a 200 amp industrial inverter MIG welder with 240v single phase input and 4-Roll wire feed
system. Ideal for automotive work with its minimum current of 30 Amps.

|
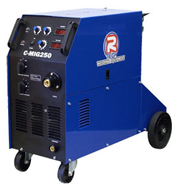 |
MIG C-MIG250 Compact
The
C-MIG250 MIG welder is a 250 amp industrial transformer MIG welder with 240v input boasting a heavy
duty 4-roll wire feed system.

|
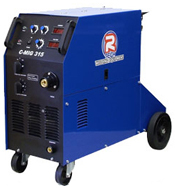 |
MIG C-MIG315 Compact
The C-MIG315 MIG welder is a 315 amp industrial MIG welder with 415v 3-phase input
boasting a heavy duty 4-roll wire feed system.

|
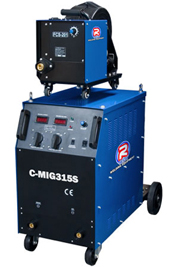 |
MIG C-MIG315s
The C-MIG315S is a 315
amp industrial MIG welder with 415v 3-phase input boasting a separate heavy duty 4-roll wire feed
system.

|
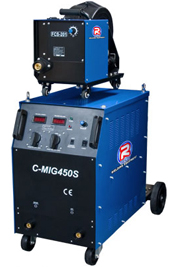 |
MIG C-MIG450s
The C-Mig450S Mig Welder
is a 450 amp industrial MIG welder with 415v 3-phase input boasting a seperate heavy duty
4-roll wire feed system.

|
R-Tech Welding Machines
Compare with Lincoln and Miller but don't cost as
much!
For great products at great prices, call us on +27 11 784
0171 or email: sales@weld-tech.co.za
Or email deon@weld-tech.co.za for technical queries.
WE SHIP TO THE FOLLOWING
COUNTRIES:
BOTSWANA, ZAMBIA, NAMIBIA, ZIMBABWE, MOZAMBIQUE,
ANGOLA.
PLUS ANY OTHER COUNTRY IN AFRICA.
Please note: Prices are Subject to
Change
What is MIG
Welding?
Gas metal arc welding (GMAW) sometimes referred to by its
subtypes metal inert gas (MIG) welding
or metal active gas (MAG)
welding, is a semi-automatic or automatic arc welding
process in which a continuous and consumable wire electrode and a shielding gas are fed through a
welding gun.
The typical MIG welding gun has
a number of key parts—a control switch, a contact tip, a power cable, a gas nozzle, an electrode
conduit and liner, and a gas hose. The control switch, or trigger, when pressed by the operator,
initiates the wire feed, electric power, and the shielding gas flow, causing an electric arc to be
struck. The contact tip is connected to the welding power source through the power cable and
transmits the electrical energy to the electrode while directing it to the weld area. It must be
firmly secured and properly sized, since it must allow the passage of the electrode while
maintaining an electrical contact. Before arriving at the contact tip, the wire is protected and
guided by the electrode conduit and liner, which help prevent buckling and maintain an
uninterrupted wire feed. The gas nozzle is used to evenly direct the shielding gas into the welding
zone—if the flow is inconsistent, it may not provide adequate protection of the weld area. Larger
nozzles provide greater shielding gas flow, which is useful for high current welding operations, in
which the size of the molten weld pool is increased. The gas is supplied to the nozzle through a
gas hose, which is connected to the tanks of shielding gas. Sometimes, a water hose is also built
into the welding gun, cooling the gun in high heat operations.
The wire feed unit supplies the
wire to the work, driving it through the conduit and on to the contact tip. Most models provide the
wire at a constant feed rate, but more advanced machines can vary the feed rate in response to the
arc length and voltage. Shielding gases are necessary for gas metal arc welding to protect the
welding area from atmospheric gases, such as nitrogen and oxygen, which can cause fusion
defects
MIG Welding can produce all
kinds of joints and welds depending upon the type of work being carried out, the appropriate
shielding gas and wire. Two types of welding method are commonly used on MIG welding machines:
Globular Transfer and Spray Transfer
Globular metal transfer occurs at relatively low operating currents
and voltages but these are still higher than those used in short circuiting transfer. This metal
transfer mode is characterised by a drop, two or three times larger in diameter than the wire,
formed at the tip of the electrode. This droplet is detached from the tip of the electrode by the
effect of a pinch force and the transfer of the droplets in irregular form across the arc is aided
by the effect of the weak electromagnetic and strong gravity forces. As the droplets grow on the
tip of the wire electrode they wobble around and disturb the arc plasma stability. Consequently,
the heat-affected zone in the work becomes narrow, penetration of the weld becomes small, and the
weld deposit is irregular and large amounts of spatter takes place
Spray Transfer occurs under an argon-rich shielding gas, increasing
the current and voltage causes a new mode of metal transfer to appear: the tip of the wire
electrode is tapped, the sizes of the droplets become smaller and they are directed axially in a
straight line from the wire to the weld pool.
|
Gas metal arc
welding (GMAW) sometimes referred to by its subtypes metal inert gas (MIG)
welding or metal active gas
(MAG) welding, is a semi-automatic or automatic arc welding process in
which a continuous and consumable wire electrode and a shielding gas are fed through a welding
gun.
The typical MIG welding gun has a number of key
parts—a control switch, a contact tip, a power cable, a gas nozzle, an electrode conduit and liner, and a gas hose.
The control switch, or trigger, when pressed by the operator, initiates the wire feed, electric power, and the
shielding gas flow, causing an electric arc to be struck. The contact tip is connected to the welding power source
through the power cable and transmits the electrical energy to the electrode while directing it to the weld area.
It must be firmly secured and properly sized, since it must allow the passage of the electrode while maintaining an
electrical contact. Before arriving at the contact tip, the wire is protected and guided by the electrode conduit
and liner, which help prevent buckling and maintain an uninterrupted wire feed. The gas nozzle is used to evenly
direct the shielding gas into the welding zone—if the flow is inconsistent, it may not provide adequate protection
of the weld area. Larger nozzles provide greater shielding gas flow, which is useful for high current welding
operations, in which the size of the molten weld pool is increased. The gas is supplied to the nozzle through a gas
hose, which is connected to the tanks of shielding gas. Sometimes, a water hose is also built into the welding gun,
cooling the gun in high heat operations.
The wire feed unit supplies the wire to the
work, driving it through the conduit and on to the contact tip. Most models provide the wire at a constant feed
rate, but more advanced machines can vary the feed rate in response to the arc length and voltage. Shielding gases
are necessary for gas metal arc welding to protect the welding area from atmospheric gases, such as nitrogen and
oxygen, which can cause fusion defects
MIG Welding can produce all kinds of joints and
welds depending upon the type of work being carried out, the appropriate shielding gas and wire. Two types of
welding method are commonly used on MIG welding machines: Globular Transfer and Spray Transfer
Globular metal transfer occurs at relatively low operating currents and voltages but
these are still higher than those used in short circuiting transfer. This metal transfer mode is characterised by a
drop, two or three times larger in diameter than the wire, formed at the tip of the electrode. This droplet is
detached from the tip of the electrode by the effect of a pinch force and the transfer of the droplets in irregular
form across the arc is aided by the effect of the weak electromagnetic and strong gravity forces. As the droplets
grow on the tip of the wire electrode they wobble around and disturb the arc plasma stability. Consequently, the
heat-affected zone in the work becomes narrow, penetration of the weld becomes small, and the weld deposit is
irregular and large amounts of spatter takes place
Spray Transfer occurs under an argon-rich shielding gas, increasing the current and
voltage causes a new mode of metal transfer to appear: the tip of the wire electrode is tapped, the sizes of the
droplets become smaller and they are directed axially in a straight line from the wire to the weld
pool.
|